반도체 전공정(웨이퍼 제작, 산화, 포토, 식각, 증착&이온주입, 금속배선, CMP)
1. 반도체 제조공정 flow
웨이퍼 제조 > 회로설계 > 마스크(레티클)제작 > 웨이퍼 가공(포토, 식각 등 8대 공정) > 조립 > TEST
1) 전공정과 후공정
(1) 전공정
- 웨이퍼 제작 및 마스크 제작, 웨이퍼 가공
- 산화>포토>식각>박막증착>금속배선
(2)후공정
- 패키징 : 웨이퍼 자동선별(EDS) > 절단 >접착 > 금속연결 > 성형
- 검사 : 최종검사 > 마킹 > 포장
2. 웨이퍼 제조 및 종류
1)웨이퍼 제조
잉곳 제조 > 잉곳절단(웨이퍼의 두께와크기는 점점 얇고 커지는 추세) > 웨이퍼 표면 연마
2)웨이퍼 명칭
- 웨이퍼 : 원형 판
- 다이 : 웨이퍼위에 있는 작은 사각형, 각각이 하나하나의 칩이 된다
- 스크라이브 라인 : 다이와 다이사이를 절단하기 위한 선
- 플랫존 : 웨이퍼의 구조를 구별하기 위해 만든 영역, 웨이퍼 가공 시 기준선이 되는 부분. 웨이퍼의 수직 수평을 판단
- 노치 : 플랫존 대신에 사용하는 기준선. 웨이퍼 보다 더 많은 침 생산 가능하여 효율이 높다
하지만 대부분은 플랫존 사용
3) 결정 구조 및 타입
(1)단결정
- 전체의 덩어리가 하나의 동일한 배열의 결정구조를 가진 결정 -> 웨이퍼로 사용 되는 결정
- 초크랄스키법으로 성장
(2)다결정
- 부분부분마다 결정의 배열이 다르게 나타나는 구조
(3)밀리 지수
- 결정 구조에서 특정한 면으로 자를때, 그 자르는 방향에 따라서 자른 면의 모양과 물리적, 전기적 특성이 다르게 나타는 것
- 반도체 결정구조를 나타낼 때 면과 뱡향을 나타냄
(4) 웨이퍼의 타입
- 플랫존이 있는 모습에 따라 구별 가능
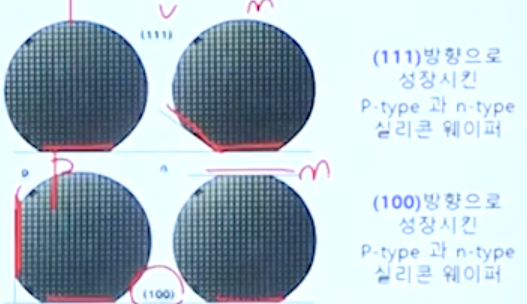
3. 산화공정
1)산화공정의 개요 및 역할
- 이산화규소막을 형성하는 단계 ->웨이퍼의 보호막 역할이 가장 주된 목표
- 이외에도 누설 전류 방지, 불순물 확산 방지, 식각 방지막 역할
- 웨이퍼에 절연막 역할을 하여 회로와 회로사이에 누설전류가 흐르는 것을 차단
- 이온주입공정에서 환산 방지막 역할
- 식각 공정에서는 다른 부분이 식각되지 않게 보호하는 식각 방지막 역할
- 공정 중 발생하는 불순물로부터 오염을 막는 역할
2) 방법
- 열산화, 화학적 기상증착산화(CVD), 전기 화학적 산화 방법이 있다
- 그 중 가장 많이 쓰이는 것이 열산화 방법 > 고온에서 가열
(1)열산화 방법 - 건식산화
- 순수한 산소를 이용하는 방법으로 산화막의 성장속도가 느려 주로 얇은 막을 형성할 때 사용
- 전기적 특성이 좋은(밀도가 높은) 산화막을 만들 수 있다.
(2)습식 산화
- 산소와 함께 용해도가 큰 수증기를 함께 사용하는 방법
- 산화막의 성장속도가 빠르고 보다 두꺼운 막을 형성할 수 있다.(동일 시간대비 5~10배 정도 두껍다)
하지만 건식산화에 비해서 산화층의 밀도가 낮아서 전기적 특성이 좋지 않다.
4. 포토공정
- 감광액 도포 > 소프트 베이크 > 노광(빛쪼이기) > 현상(PR제거) > 하드 베이크 > 검사
1)감광액 도포 > 소프트 베이크
- 웨이퍼 표면에 빛에 민감한 물질인 PR을 도포하는 작업
- 얇고 균일하게 도표하여 감도를 높인다
- PR코딩 전 HMDS 사용(접착제 역할)> 웨이퍼 표면을 친수성에서 소수성으로 바꿔주는 역할 > 그 후 스핀코팅으로 통해 PR을 도포하고 소프트베이크를 통 솔벤트 성분을 제거(솔벤트는 빛을 흡수하는 성질이 있기 때문에)
※PR의 세가지 물질 : 솔벤트(휘발성, 레진(폴리머), Photoactive compound(빛에 반응하는 화합물)
양성 PR: 노광 되지 않는 영역을 남기는 -> 마스크와 동일한 현상
음성 PR : 노광된 영역만 남김 -> 마스크와 반대되는 현상현상
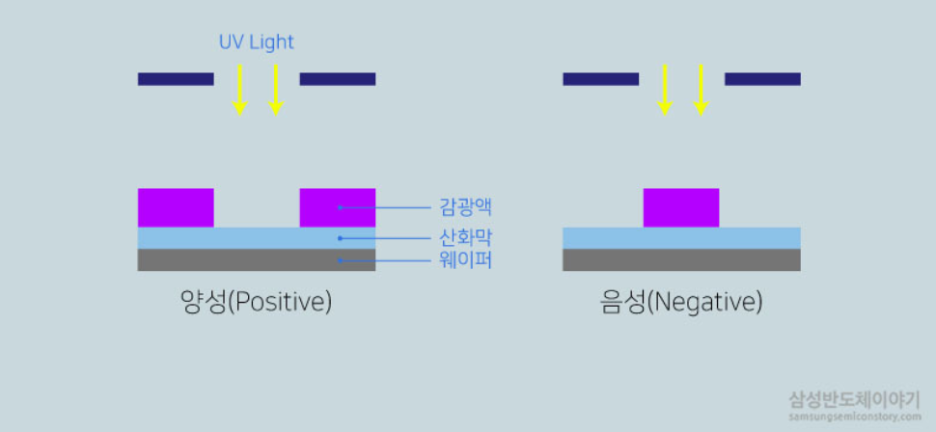
2)노광 공정 : 빛을 통해 웨이퍼에 회로를 그려 넣는 공정
- 노광장비(Stepper)를 사용해 회로 패턴이 담긴 마스크에 빛을 통과시켜 웨이퍼에 회로를 형성.
3)현상공정
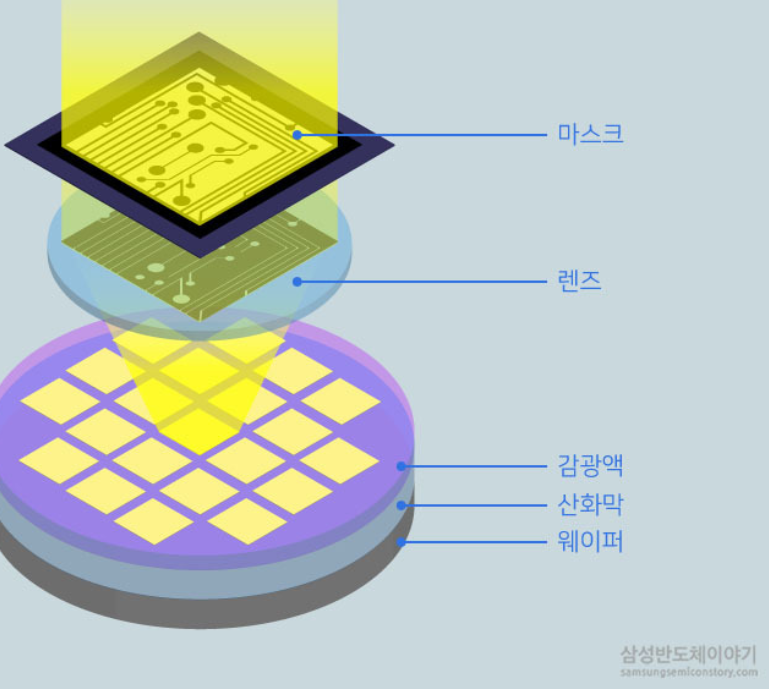
- 현상 공정 : 회로 패턴을 형상
- 웨이퍼에 현상을 뿌려가며 노광된 영역과 노광되지 않는 영역을 선택적으로 제거하여 회로 패턴을 형성
※하드베이크
- 현상 후 감광액을 굳게하고 기판에 잘 접합시키는 공정(잔여 solvent 제거 및 접착도 증가)
5) 노광법의 종류
(1)접촉식 노광
- Mask와 Wafer를 밀착하여 노광하는 방식
장 : 단순, 저가, 회절효과 최소
단 : 오염에 의한 Mask 손상
Wafer : mask = 1:1
(2)근접식노광
- Mask와 wafer의 간격을 일정하여 유지하여 노광하는 방식
- 오염 및 Mask 손상없음 but 회절(diffraction)발생 및 고가
wafer : mask = 1:1
(3)투영식 노광
- Reticle 상의 패턴을 통해 노광하는 방식(stepper)
- 오염 및 mask 손상 X, 미세패턴 형성 가능
- 복잡, 고가 및 노광시간이 길다
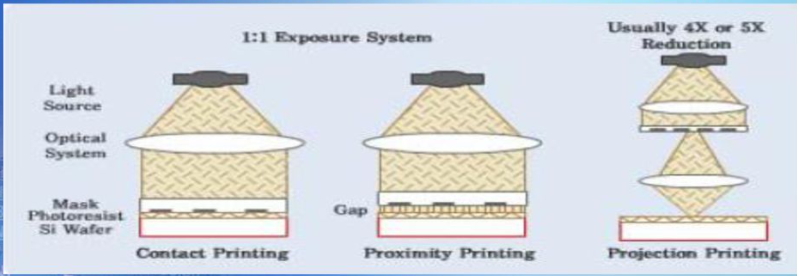
6) 포토 공정 주요 인자
(1)분해능(해상도)
- 최소 선폭의 한계
- 웨이퍼 표면에 조사할 수 있는 최소의 크기로 작을 수록 더 작은 선폭으로 표현할 수 있으므로 작을 수록 좋다.
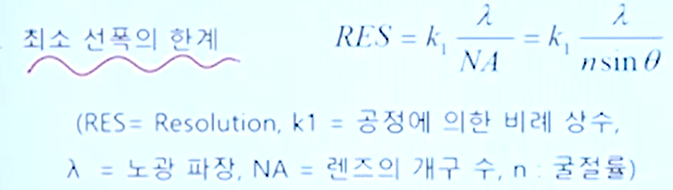
- NA : 렌즈의 개구수
- 개수는 렌즈의 상대적 크기 = R/F = n sin(theta)
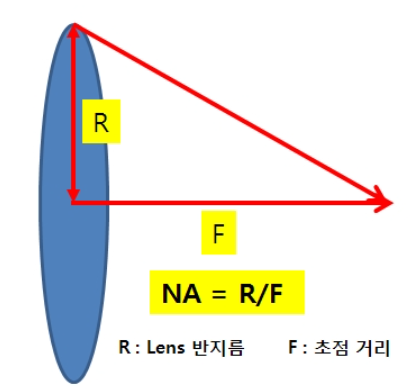
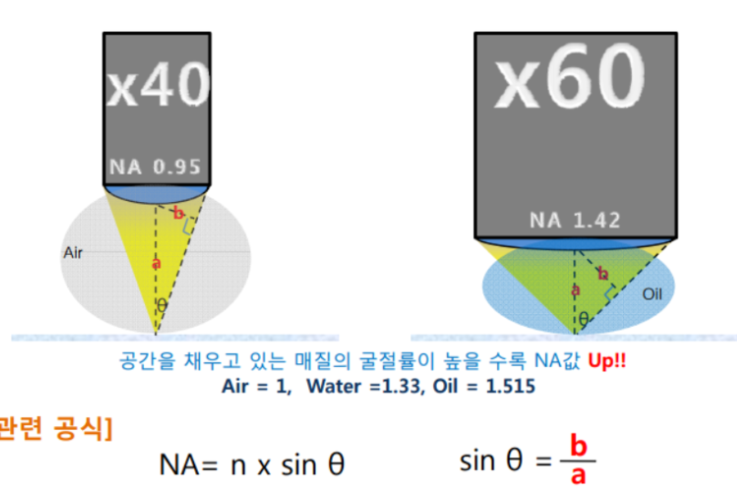
(2) DOF(초점심도)
- 렌즈나 반사거울 등에서 어떤 점 P0의 상을 P0'에 맺게 할 때 상 쪽 P0' 앞 뒤의 선명하게 보여지는 범위로 클수록 여유가 존재해서 패턴 형성이 용이 > 클수록 좋다.
- NA가 거지면 DOF가 줄어들고 NA가 작아지면 DOF가 커져서 분해능과 trade off 관계
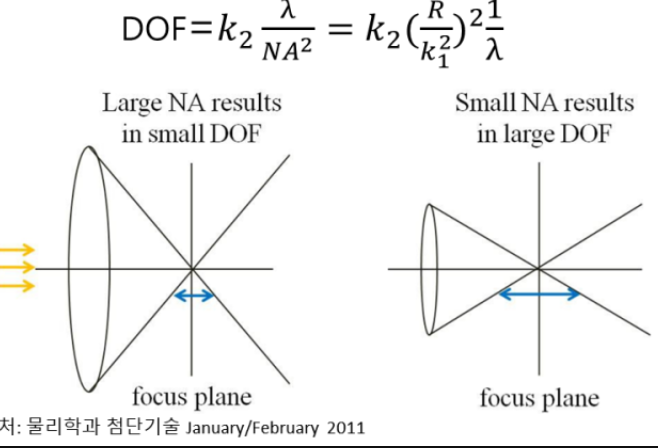
1. 식각공정
1) 식각공정 개요
- 포토 공정 후 필요한 회로 패턴을 제외한 나머지 부분을 제거하여 반도체 구조를 형성하는 공정
- 웨이퍼에 액체 또는 기체의 부식액을 이용해 불필요한 부분을 제거하여 회로패턴을 만드는 과정
2) 공정 순서
- 포토공정에서 형성된 감광액 부분을 남겨두고 산화막의 나머지 부분을 부식액을 이용해 제거하여 회로(패턴을 형성 식각이 끝나면 감광액을 제거(포토 스트립, ashing)
- 이와 같이 반도체를 구성하는 여러 층의 얇은 막에 원하는 회로 패턴을 형성하는 과정을 반복
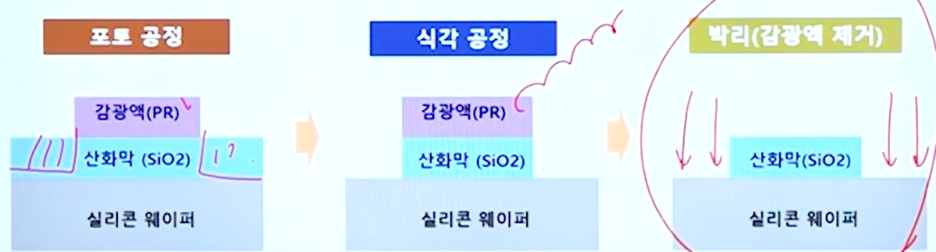
- 이 다음에 불순물을 투입
3) 건식 식각 습식 식각
건식
- 반응성 기체, 이온 등을 이용해 특정 부위를 제거하는 방법
- 느리다, 이방성의 장점 -> 미세 패턴 형성에 용이, 비싸고 방법이 어렵다, 플라즈마 이용
※플라즈마
대기압 보다 낮은 압력인 진공챔버에 가스를 주입한 후 전기 에너지를 공급하여 플라즈마를 발생
플라즈마는 물질의 제 4의 상태로 많은 수의 자유전자, 이온, 중성 원자로 구성된 기체
※이온화
전기적으로 중성인 원자 또는 분자에 전자들이 떨어져 나가면서 이온상태가 되는 현상
습식
- 용액을 이용해 화학적인 반응을 통해 식각하는 방법
- 빠르지만 동방상 > 미세 패턴 형성에 어려움
4) 플라즈마의 발생
- 충분한 전기에너지를 통해 자기장 형성 > 기체들이 가속을 받아서 충돌
> 자기장이 자유전자를 가속화시켜 높은 에너지를가진 자유전자가 중성의 원자나 분자와 충돌하여 이온화
> 이것이 연쇄 반응을 일으켜 이온의 수가 급격하게 증가하여 플라즈마 상태가 된다.
플라즈마 발생시 양이온과 전자는 반드시 쌍으로 발생하기 때문에 플라즈마는 전기적으로 중성인 상태를 유지
5) 건식 식각의 주요 인자
균일도 유지(uniformity)
- 웨이퍼 상 여러 지점에서 얼마나 동일하게 식각이 되는가
- 부위별 칩의 특성을 동일하게
식각 속도
- 일정 시간 동안 얼마나 제거할 수 있는지
선택비
- mask의 박막과 식각하는 박막의 etch rate 비율
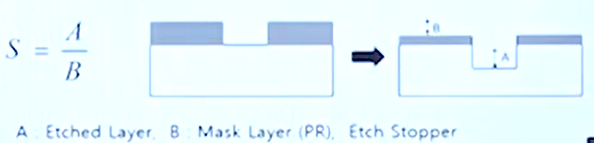
- PR두께를 두껍게 하여 조절
etch profile
2. 박막공정
- 박은 1마이크로미터 이하의 얇은 막
- 증착공정은 웨이퍼 위에 원하는 분자 또는 원자 단위의 물질을 박막의 두께로 입혀 전기적특성을 가지게 하는 공정
물리적 기상증착방법(PVD)
금속박막의 증착에 주로 상용되며 화학반응이 수반되지 않음
스퍼터링법(sputtering), 기화법(열기화법, e-beam기화법)
화학적 기상증착방법(CVD)
가스의 화학반응으로 형성된 입자들을 외부 에너지가 부여된 수증기 형태로 쏘아 증착시키는 방법. 도체, 부도체, 반도체의 박막증착에 모두 사용될 수 있는 기술
1)물리적 기상증착 방법(PVD)
스퍼터링법
- 강한 전압을 가하여 자유전자와 Ar기체 간의 충돌로 플라즈마 발생 > Ar기체가 Ar+ 이온화가 되어 전압이 가해진 Target 기판에 충돌 > 충돌 후 튀어나온 증착물질들이 +전압이 가해진 증착기판에 증착하는 방식
열기화법
- 증착시키고자 하는 물질을 보트에 올려두고 가열함으로써 증착물질을 증발시켜 기판에 증착하는 방식
전자빔 기화법
- 증착시키고자 하는 물질을 보트에 올려두고 전자 빔을 이용하여 증착물질을 가열하는 증착방식
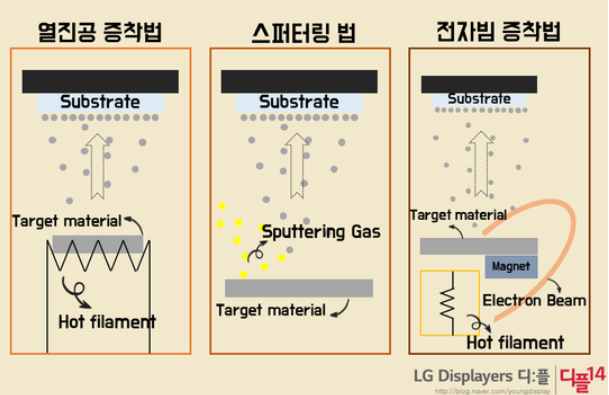
2)화학적기상증착방법(CVD)
LPCVD : 고품질, 높은 생산량 하지만 속도가 느리다.
PEDVD : 저온과 고속증착의 장점, 하지만 품질의 낮다.
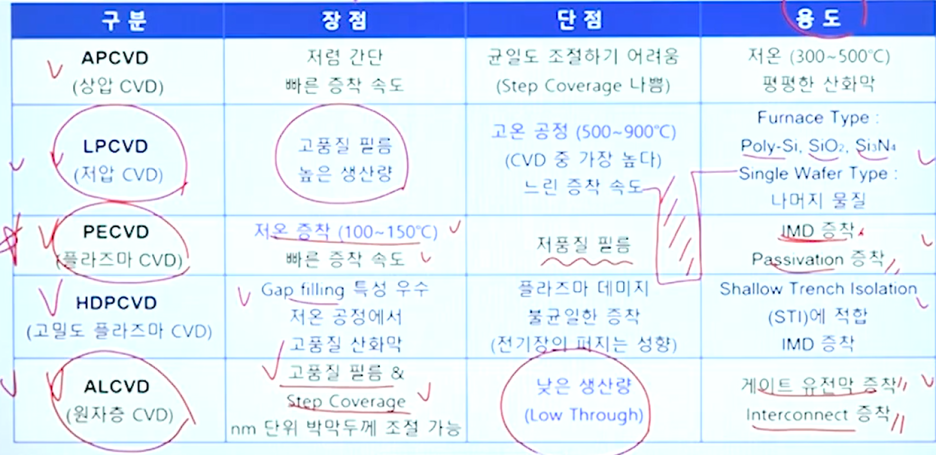
3) 박막공정 주요인자
품질 : 전기적 특성, 물리적 특성의 품질
두께 균일도 : 웨어퍼내 균일도, 웨이퍼와 웨이퍼 간의 균일도
스탭 커버리지(step coverage) : 단자에서의 일정한 박막두께 유지
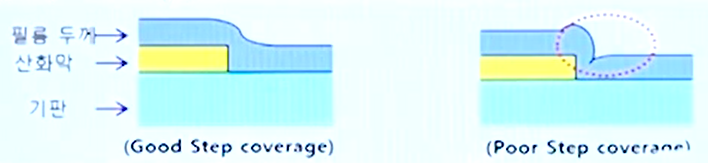
종회비 : height / width의 비
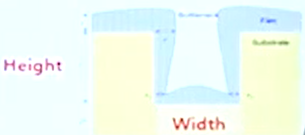
필링 : 단자사이의 공간을 잘 채우는지의 척도
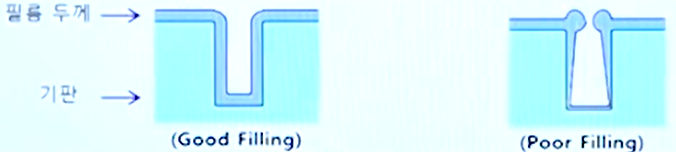
3. 불순물 주입 공정
1) 도핑 방법
- 열 확산 방법
- 열을 주입하여 도핑물질을 확산시켜 도핑하는 방법. 등방성 성질로 도핑하려는 부분을 정학하게 도핑하지 못하고 옆 부분까지 도핑
2) 이온주입법
- 도핑 물질을 이온화 한 후 가속하여 운동에너지를 이용해 강제로 주입하는 기술
- 이방성의 성질로 정확성이 높다.
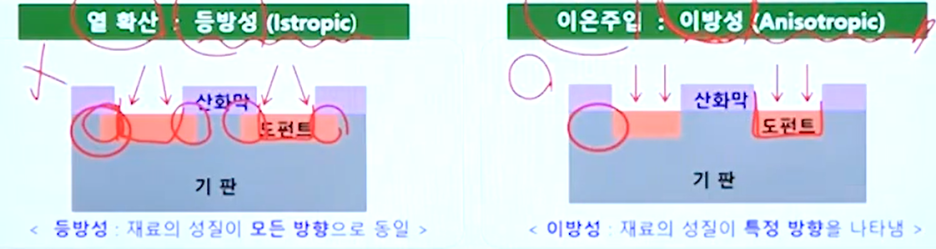
(1)이온 주입
- 반도체 웨이퍼내에 불순불(붕소, 인, 비소 등)을 이온화된 상태로 주입시켜 반도체가 특정한 전기적 특성을 갖도록 하는 공정
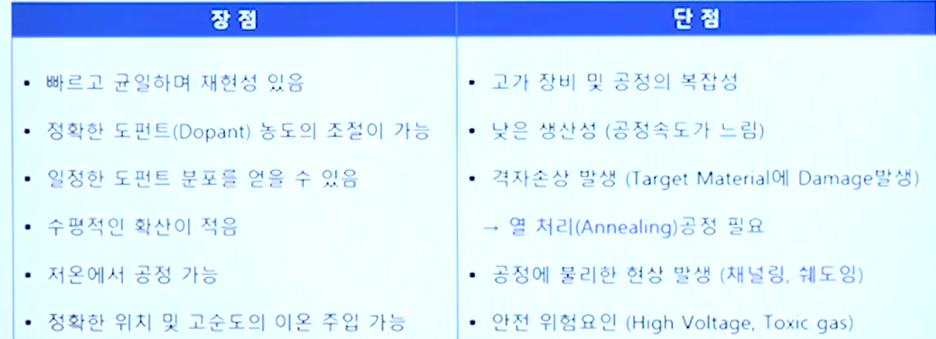
(2) 이온 주입 장치의 구성 및 원리
- 원하는 이온을 형성하는 이온소스, 이온을 고 에너지 상태로 가속시키는 가속기, 이온이 충돌을 일으키는 다켓 챔버로 구성
※이온주입의 원리
- 전기적으로 중성인 공정 가스(불순물)에 전자를 충돌시켜 가스가 전자를 잃어 양이온을 만들고 여러 이온 중에서 에널라이저(Analyzer)을 통해 최종적으로 주입될 이온만 선택(Ion Beam)
- 이온 빔을 높은 전압으로 가속시켜 타켓 챔버 내에 웨이퍼에 도달
- 이온의 에너지는 가속전압에 따라 결정되고 이를 통해 불순물의 도핑 양과 깊이를 조절
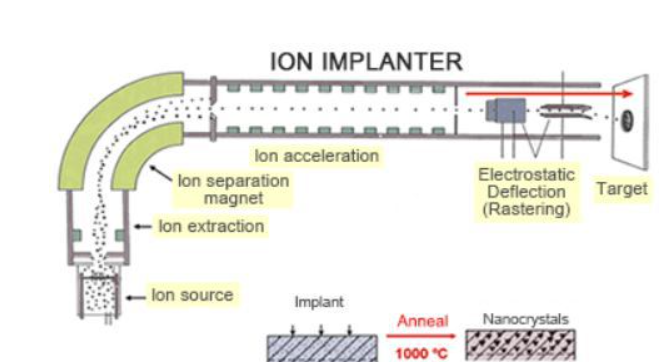
(3) 이온 주입 문제점 및 해결책
채널링 현상
- 이온이 더 깊숙이 도달하는 현상
- 웨이퍼(기판을) 어느 정도(7도정도) 틀어서 공정 진행
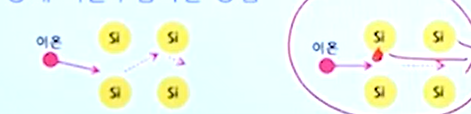
쉐도잉 현상
- 다른 구조에 가로막혀 그 부분에 이온 주입이 되지 않는 현상
- 웨이퍼(기판)을 어느 정도(7도정도) 틀어서 공정 진행
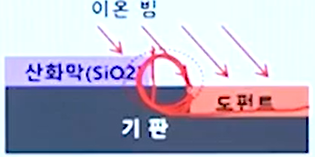
(4) 열처리 공정(Annealing)
이온 주입 후 문제점
- 강한 에너지에 의한 이온 주입으로 기판 결정에 damage발생
주입된 이온은 기판내에 치환위치에 올바르게 위치해여 캐리어로서의 역할을 잘 수행할 수 있는데 결정 구조가 변경되고 다른 곳에 위치하게 되는 문제 발생
-> 어닐링을 통해 불순물을 재위치
아닐링의 목적
- 결함이 발생된 기판을 재결정시키기 위함
- 주입된 이온이 결정 속의 치환 위치로 이동되어 도핀트로서의 역할을 하게 하기 위함
6)열처리 공정 방법
annealing 공정(열처리 공정)
높은 온도를 가해 실리콘 원자 사이에 들어온 불순물들이 원래있던 실리콘과 치환하여 잉여전자 또는 잉영 정공을 형성하여 전기적특성을 하는 공정
Furnace annealing
일반적으로 사용하는 방법으로 고온으로 가열
장 : Batch type으로 여러 장의 wafer 처리 / 단: 열처리량 증가, 오염 가능성 및 오랜 공정시간
RTP(Rapid Thermal Process)
텅스텐 할로겐 램프의 포톤 에너지가 결정에 흡수됨으로서 이닐링온도를 높여 열처리
>공정제어가 용이하고 빠른 공정가능
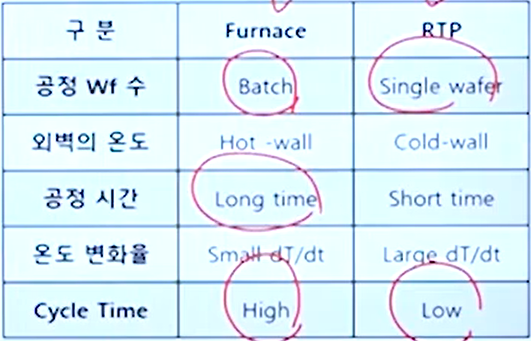
1. 금속 배선 공정
- 전기가 잘 통하는 금속의 성질을 이용하여 반도체의 회로패턴을 따라 전기 길, 즉 금속선을 이어주는 과정
2. 금속 배선 공정 증착방법
1)물리적 기상증착 방법(PVD)
- 진공증착
고진공 상태에서 알루미늄을 증기화하여 부착
- 스퍼터링
플라즈마를 이용한 증착
2)화학적 기상증착 방법(CVD)
금속 배선의 연결 부분인 접점의 크기가 좁은 구멍에는 알루미늄보다 텅스텐을 많이 사용
균일하게 박막을 형성해 부착시키기 위해서는 진공증착보다 화학적 기상증착방법을 사용
3. 금속 배선 공정의 금속재료 필요조건
- 반도체 기판(웨치퍼)과의 부착성
- 전기저항이 낮은 물질
- 열적, 화학적 안정성 : 후속 공정에 의해서 열, 화학 반응에 의해 특성이 변하지 않을 것
- 패턴 형성의 용이성
- 높은 신뢰성 : 끊기지 않고 오래 갈수 있을 것(수명)
- 제조 가격
4. 반도체용 금속배선
1) 배선의 종류
Plug : 단위소자 전극에 직접 연결되는 배선
Local interconnect : 근접된 소자 사이를 연결하여 하나의 logic unit을 형성
Via : 각 배선층 사이를 수직으로 연결
Global interconnect : 각각의 logic unit을 연결하여 전체적인 신호를 전달하는 배선
2)반도체용 금속배선의 종류
실리사이드
- Si이 금속과 반응하여 현성된 화학적으로 안정된 물질을 실리사이드라고 한다.
응용부분
- 실리콘과 금속배선 사이에 사용되어 전기저항 및 접촉저항을 감소시킴
- ocal interconnection에 사용
- 그 자체로서 확산방지막의 역할
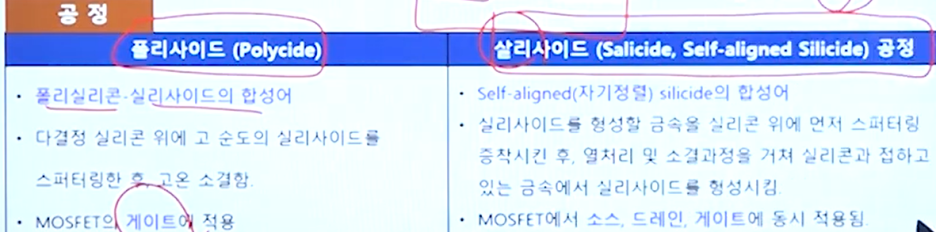
폴리사이드 공정 : mosfet에 게이트 사용
실리사이드 : 소스, 드레인, 게이트까지 동시에 적용 가능
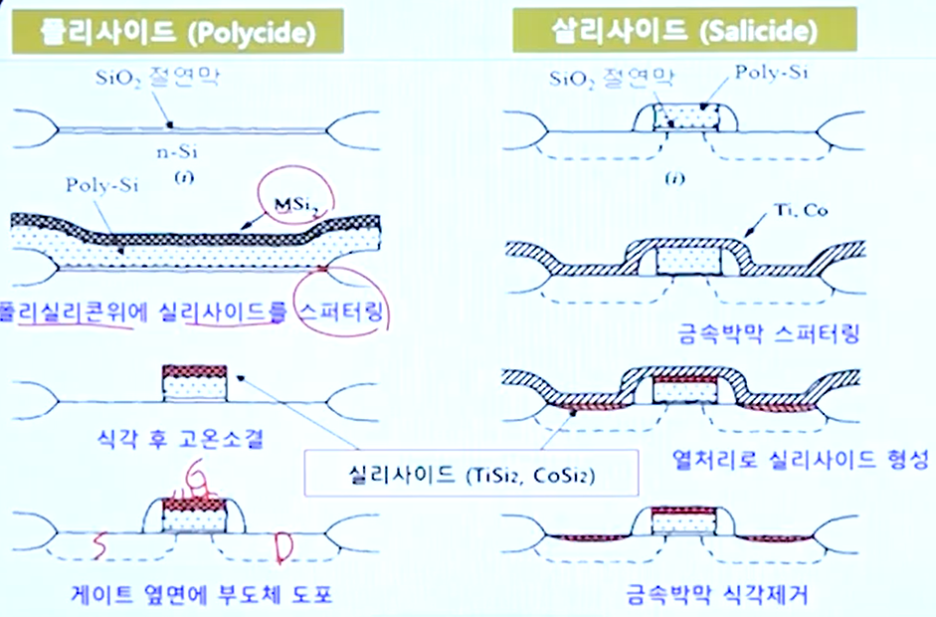
플러그 및 via
- 금속배선과 소자를 연결하는 역할
- 일반적으로 중간 절연물에 윈도우(절연물질을 파 만드는 홈)를 만들어 금속을 채워서 제조
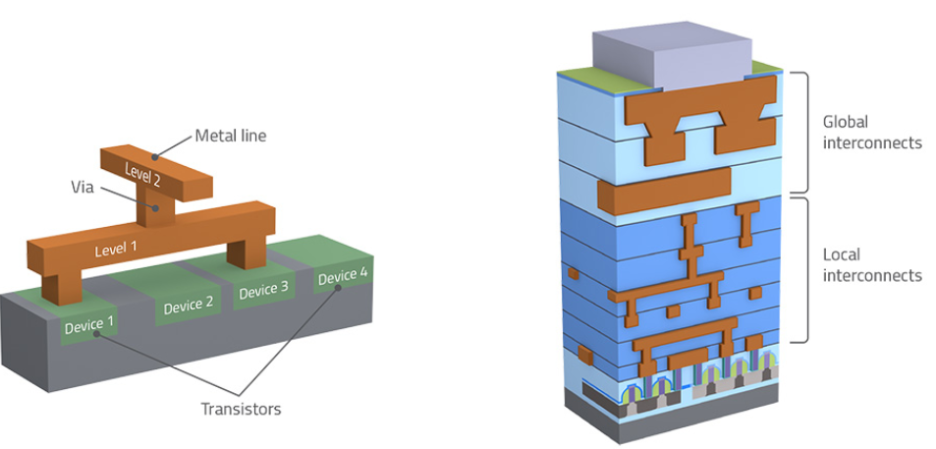
텅스텐(W)플러그(Plug)
- CVD공정으로 선택적 W 증착 공정
-Si이 노출된 위치에 W이 선택적으로 핵생성됨
- 수소를 이용하여 추가 상장
- W전면 증착후 선택적 제거 고정
- TiN을 플러그에 증착
- CVD공정으로 W전면 도포함
- CMP공정으로 윈도우 이외 영역의 W제거
3) Ai 금속배선의 문제점 및 대책
(1)junction spiking
알루미늄과 실리콘이 만나는 계면에서 서로 섞이려는 성질로 알루미늄 배선 공정에서 접합면이 파괴되는 현상
파괴현상을 방지하기 위해 두 접합면사이에 장벽(베리어 메탈)에 해당하는 금속을 증착하는 과정을 추가
베리어 메탈 : Al내에 미리 si를 첨가하여 박막을 형성해 접합면 파괴를 방지

(2)Elector Migration
금속 내부에 전자간 충돌에 의한 전기적 이동이 발생하여 금속 배선에 void가 발생>al 내에 Cu 첨가하여 확산 방지
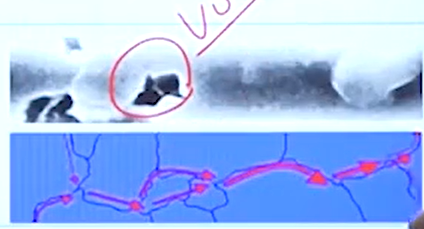
4)금속배선의 개선 방향
좁은 영역에도 금속을 잘 채우기 위해 CVD으로 전환
기존의 도선재료(Al,W)보다 저렴하도 전도성이 우수한 Cu사용
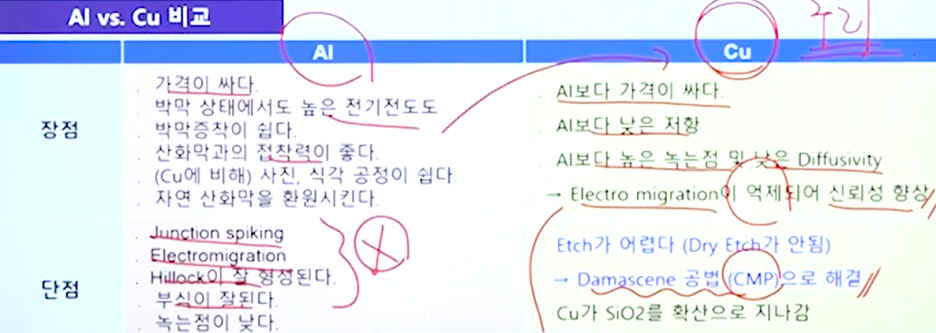
5)Cu 금속 배선의 다마신 공정
다마신공정(상강기법)
절연물질을 패터닝 공정을 통해 식각하여 홈을 형상한 뒤 전해 도금방법으로 구리르 채운 후 불필요한 부분을 연마하여 제거하는 공정(전기분해를 통해 Cu증착)
순서
a,b : 절연물에 배선모양으로 홈을 식각
c : 확산 방지층 증착 및 Cu seed층 증착
d : Cu 도금 e : 도출된 Cu CMP로 제거 f : capping layer 형성

2. CMP공정
- CVD 공정 이후 웨이퍼 표면을 화학적, 기계적 방법을 이용하여 평탄화 하는 공정. 표면 골국 감소
CMP공정원리
플래튼(platon)위에 골곡이 있는 Pad가 있고 CVD공정을 거친 wafer를 캐리어에 부착시켜 압력을 가하면서 회전시키는 방식으로 진행. Slurry용액을 투하하여 화학적, 기계적으로 연마되는 방식
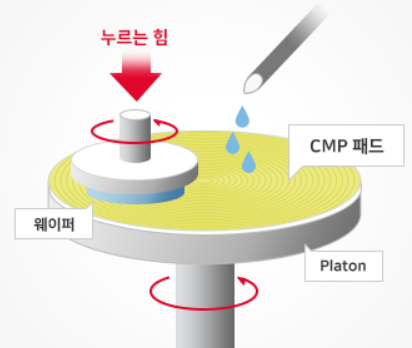
1)CMP공정 구분
Oxide(절연막) CMP, Metal CMP, Poly CMP로 구분
Oxide CMP
CVD를 통해 형성된 절연막의 단차를 낮추거나 평탄화하는 공정으로 STI CMP와 ILD/IMD CMP로 나눠지며 STI의 난이도가 상대적으로 노다
Oxide CMP는 막질이 약하기 때문에 Scratch와 Defect 발생이 쉬어 Oxide Buffing CMP 공정이 추가되어 사용
Poly CMP
Oxide CMO와 유사한 목적으로 사용
Metal CMP
텅스텐(W) CMP와 구리(Cu) CMP로 나눠지며 3D NAND 배선공정증가로 시장 성장 전망
2) CMP적용 분야
CMP 공정기술 적용 분야(3DNAND, FinFET 공정이 주요시장)
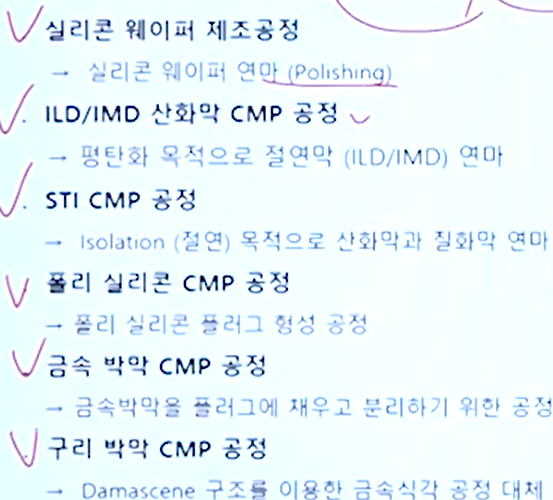
CMP공정의 장점
다층배선 및 0.2마이크로미터 이하의 광역 평탄화 가능
공정수 감소 가능
비 평탄도에 기인한 이물 감소
막 표면에 존재하는 결함제거 가능
CMP공정의 단점
CMP자체의 공정변수가 많음
>기계적인 신뢰성 패드, 슬러리 등
패턴 향상에 의한 효과를 고려해야 함
CMP에 의한 스크래치 발생 가능성이 높음 > 생산비용이 비쌈
CMP시장
구성 : CMP장비, 슬러리, 패드, 드레서
3) CMP공정에서의 Dishing
Cu CMP과정에서 Cu와 SiO2의 서로 다른 재료의 물성차이로인해 removal rate 차이가 발생하고 이로 인해 Cu가 SiO2보다 많이 깎여 나가는 현상

Cu-Cu 본딩 공정 과정에서 범프 표면 전체가 서로 맞닿지 못하고 범프 테두리에서만 본딩이 이루어짐.
이 경우 충분한 본딩강도를 얻을 수 없어 연삭과 같은 후속공정에서 웨이퍼가 떨어지는 등의 문제를 야기
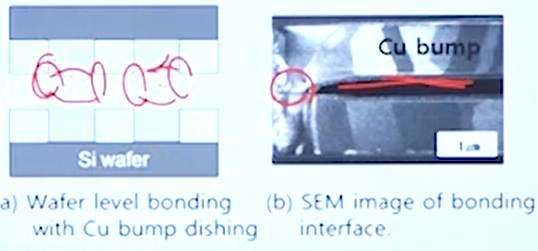