부도체 : 에너지갭이 큰 물질
도체 : 에너지갭이 없거나 작은 물질. 전도띠와 가전도띠가 겹쳐잇음
반도체 : 에니지갭이 작아서 인위적으로 전자를 전도띠로 쉽게 올릴 수 있는 물질
1. Metal line 식각
Metal : 전류 전달이 목적
dry etching이 안되는 금속 배선 방법
1)기판 -> 금속 -> 에칭 -> 절연층 도포
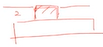
2) 기판 -> 절연층도포 -> 에칭 -> 금속채우기 -> CMP로 평탄화

- 2번을 많이 사용-> etch가 안되는 금속(구리)은 절연층을 etch하고 빈 공간에 도금을 하는 방식을 사용
- 알루미늄은 dry etch 가능
정리
metal etching = 평면상에서 금속 배선의 연결을 위하여 식각 : 보통 메모리소자처럼 알루미늄을 도선으로 사용하는 소자에서 사용하고 구리를 사용하는 비메모리 소자에는 금속을 깍기보다는 절연체를 식각하여 도금한다.
2. Cleaning, Ashing
1)cleaning
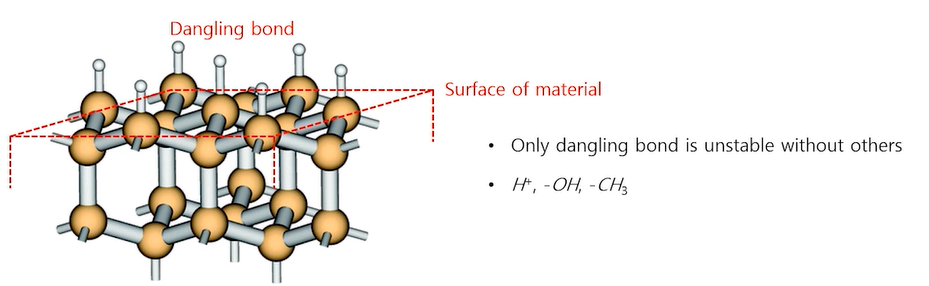
Dangling bond 부분에 다음 재료가 잘 붙을수 있도록 수소기를 붙여주는 작업
2) Ashing(포토 스트립)
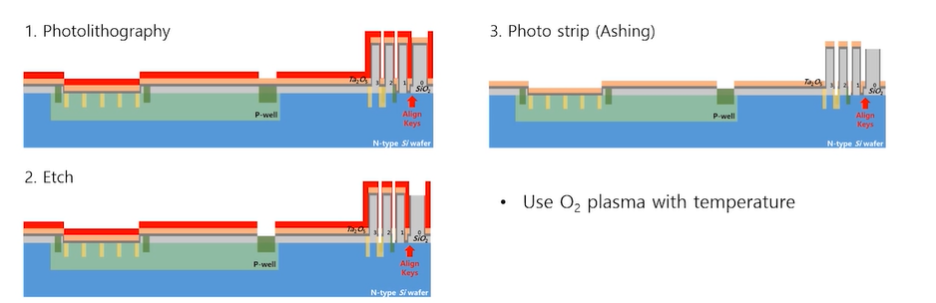
etch 후 필요없는 PR을 제거하는 과정
- Cleaning과 Ashing은 어떤 것을 제거한다는 점에서 넓은 의미의 etching에 해당되지만 그 정의는 다르다.
※RF power는 Matcher가 필요하다.
DC : 직류, AC 교류 , RF
식각의 주요 지표
1. 식각율(etch rate)
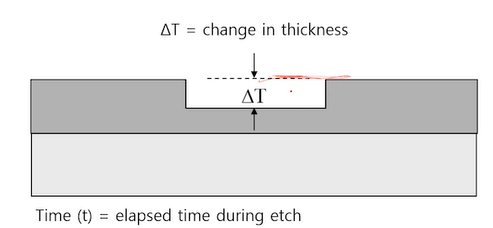
= 깍은 깊이 / 시간
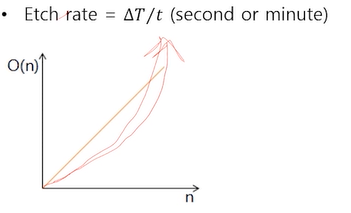
- 표면이 딱딱해서 처음에는 느리다가 점점 증가
- wet etch를 할 때
온도를 높으면 속도가 증가하지만 등방성 식각
온도를 낮추면 속도는 느리지만 이방성 시각
2. 식각 모양 : profile, bias, undercut, slop
- 이방성으로 원하는 모양으로 깎이는지에 대한 정도를 확인
- CD사이즈가 작아지다 보니 순도를 높여 etch
3. Selectivity
S = 산화막 식각 깊이 / PR식각 깊이
4. Uniformity
- 식각된 깊이가 일정한지에 대한 확인
- 깊이가 다르게 되면 플라즈마 식각이 일어날 때 플라즈마가 맞고 튀면서 다른 곳에 식각이 진행될 수도 있음.
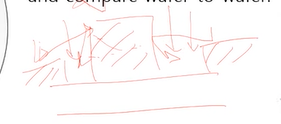
5. Residue
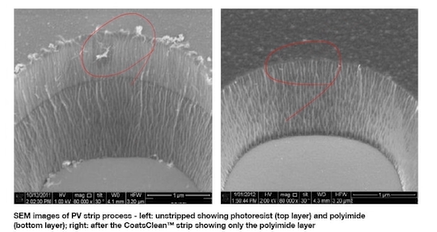
- dry etch 후 잔여물 제거를 위해서 wet etch를 통해 제거
- 파티클을 제거는 프로파일에 상관없기 때문에 wet을 통해 제거(싸고 간단)
6. 폴리머구조 생성
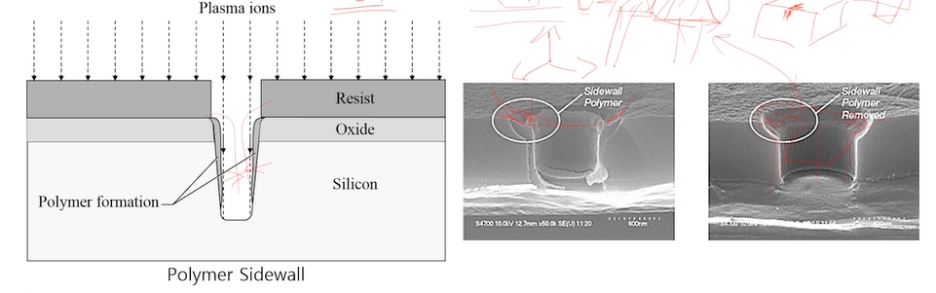
- C2F4를 사용할 때 생성-> 폴리머 구조를 활용할 수 있는지 확인
- 오히려 등방성 식각을 하게 된다.
7. 플라즈마 데미지
플라즈마는 반도체에 가해지는 온도를 줄이기 위해 사용
하지만 플라즈마로 인해 타는 현상이 생김. 파워, 챔버, 재료를 바꾸는 방법으로 버닝을 피한다.
8. 오염과 결함
오염이 마스크하여 에칭에 결함이 발생할 수 있다.문제가 생긴다.
※플라즈마와 외벽 사이의 공간에 sheath가 형성되며 에너지가 상대적으로 강한 양이온만이 이를 뚫고 식가을 진행한다.
반도체 제조 공정
= 자연 환경에서 재료가 조합되는 상황을 인위적인 환경 내에서 제어를 통해 동일한 특성을 재연하는 것
> 따라서 챔버 구조의 재료적, 기계적, 전기적 및 기하학적 특성 고려
1. chamber
- 인위적인 환경 조성과 제어 목적
- Chamber가 둥근 이유 => 플라즈마는 자연상태에서 구체 형태를 띄기 때문에 chamber도 둥글게 형성 sheath를 일정하게 만들어주기 위해서
2. 가스
reactant gas : etchant gas
purge gas : 챔버 내의 환경을 다시 리셋 시켜주는 가스.
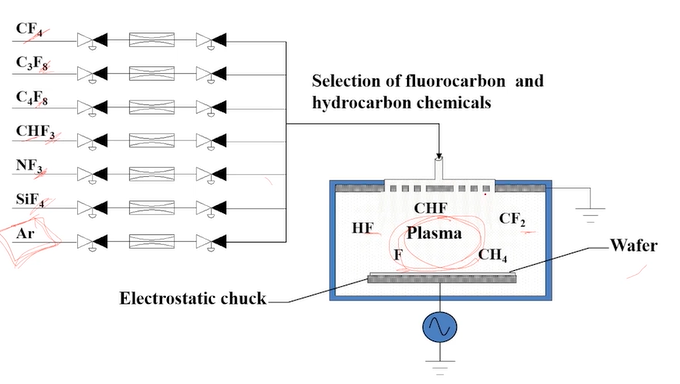
F : 플루오린 -> Si산화막과 결합하여 기체형태로 날아가게 된다. -> 화학적식각
Ar : purge gas
3. Gas Control(MFC) -> mass flow control
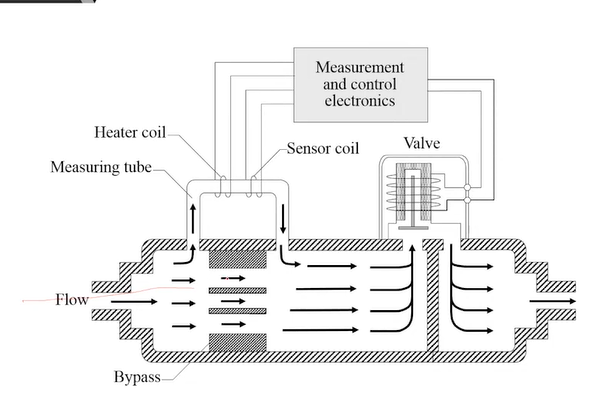
모세관으로 들어오는 기체에 열을 가하여 두 부분에 온도차이를 통해 유량 계산 -> 그 결과를 통해 벨브를 열고 닫아 유량 조절
4. 공정 압력
1기압 = 760 Torr = 1013.3 mbar = 101325 Pa = 14.696 psi
mean free path = 전자 사이의 거리를 조절하기 위해 진공을 조절하여 충분한 거리 확보
Vacuum gauge
이온에 열을 가해서 그 전자의 진동수를 체크하여 진공을 측정
5. 공정 파워 / 공정 변수 정리
DC power supply
RF power generator
-> Chamber의 Capacitance를 보정하는 역할 = matcher(또 다른 Capacity)
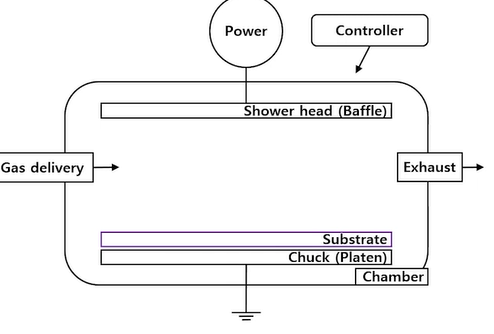
1. 플라즈마
: 기체에서 에너지를 더 가해서 이온화 시킨 해리된 물질의 상태
ex) 번개
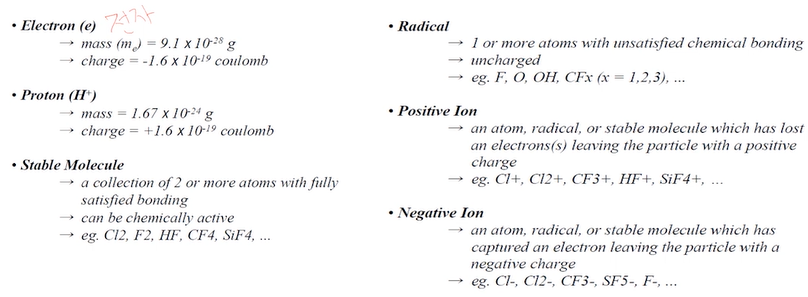
- 불활성 기체 : Cl2, F2, HF, CF4, SiF4 -> 해리 됬을 때 반응성이 좋아서 많이 사용
- Radical : 불안정한 결합 상태의 원자 -> 반응성이 큰 원자 -> 다른 물질들과 반응을 한다.
2. CCP
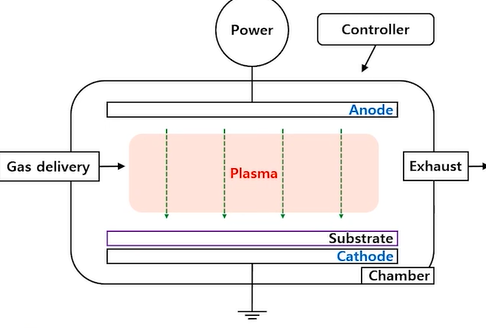
CCP 이온밀도 낮다 but 균일도 높다.
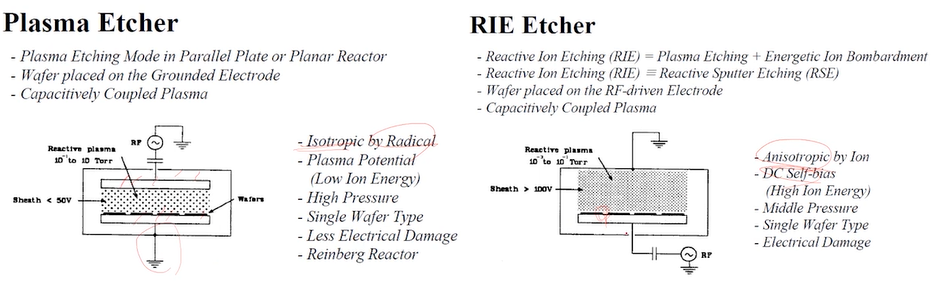
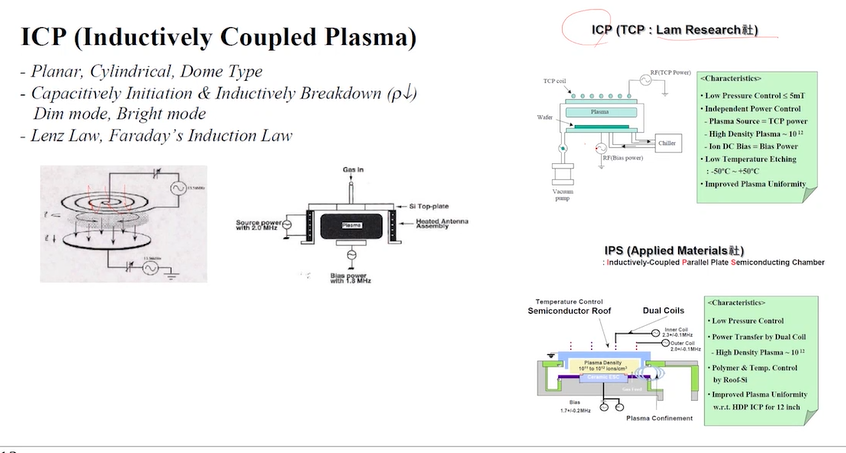
※Direct plasma는 웨이퍼가 위차한 챔버 내에서 플라즈마를 만들어 공정한다.
플라즈마의 활용
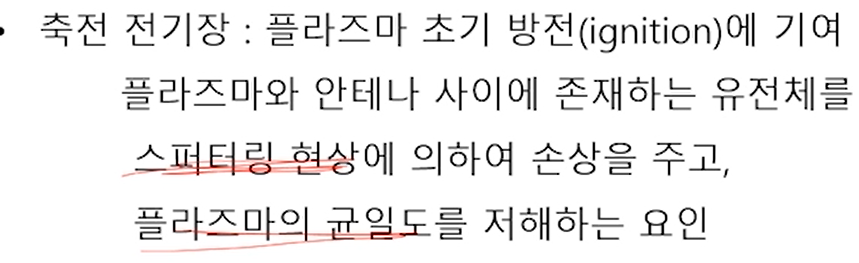
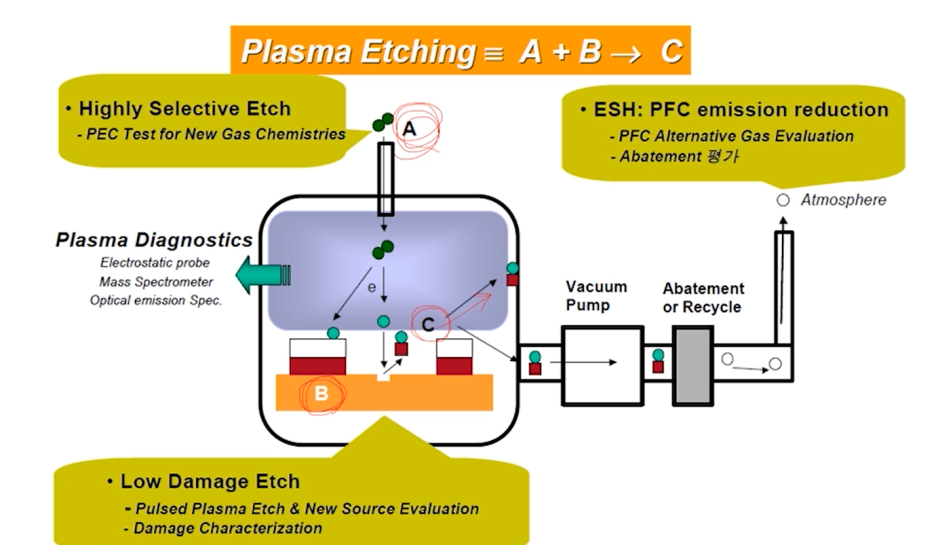
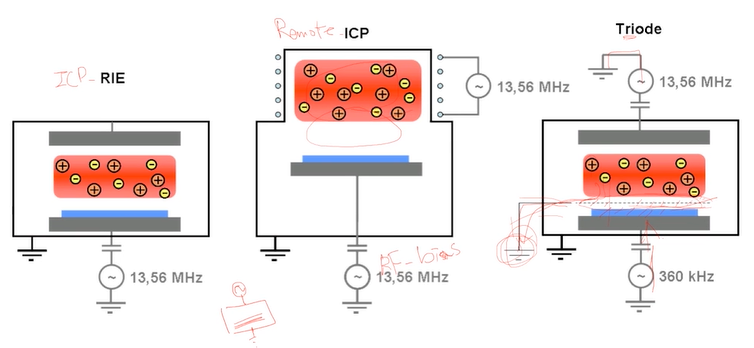
RIE : Chuck 근처에서 플라즈마를 형성하여 이온 밀도나 식각률을 높여줌
Remote ICP : 멀리서 만들어서 균일도를 높여주고 아래에도 power를 걸어주고 식각이 잘 되도록함
Triode : 전극이 세 개, sheath 쪽을 접지 시켜서 전자가 잘 바져나오게. 이를 통해 sheath에 전자를 없애서 양이온이 에너지를 전자에게 안뺏기고 잘 식각되게 한다.
※계측공정은 반도체 단위 공정에 포함되지 않는다.
1. Wet etch profile
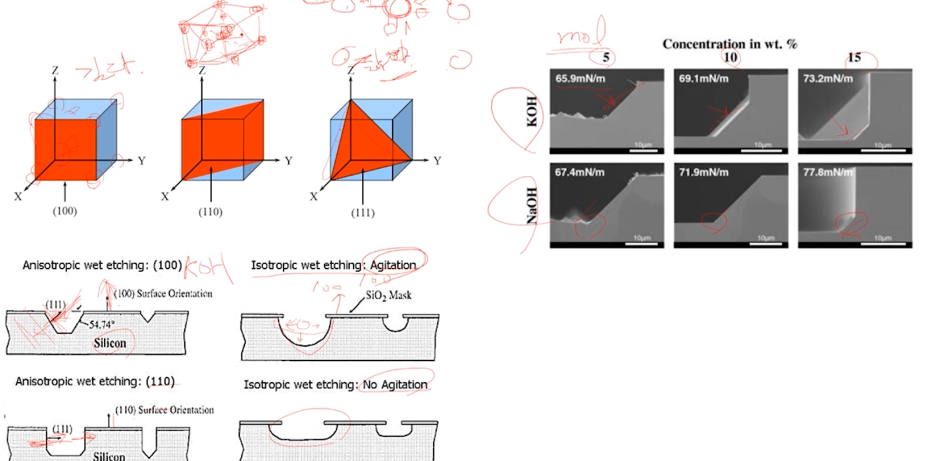
재료의 결합구조에 따라 식각 모양이 다름
dipping : etchant의 표면장력이 강하고 면을 etch할 때
spray : CD사이즈가 작고 etchant의 표면장력이 작아 모세관 현상이 발생해 dipping 안될 때
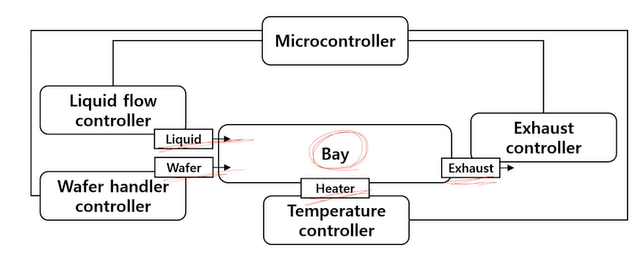
포토스트립도 습식으로 진행 가능
2. 습식 공정의 주요 변수
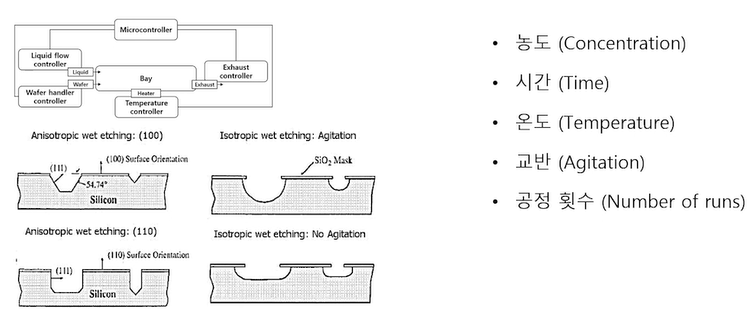
건식
- 축전기 두 극판을 가깝게 붙여놓은 것
-양성자가 sheath를 통과할 만큼 충분한 power 공급
- 전자의 충돌에너지를 통해 플라즈마의 포텐셜 에너지를 올려줌
bias : 플라즈마를 잡아 당겨주는 역할
sheath : 전자가 없어서 방출하는 빛이 없어 어두운 부분
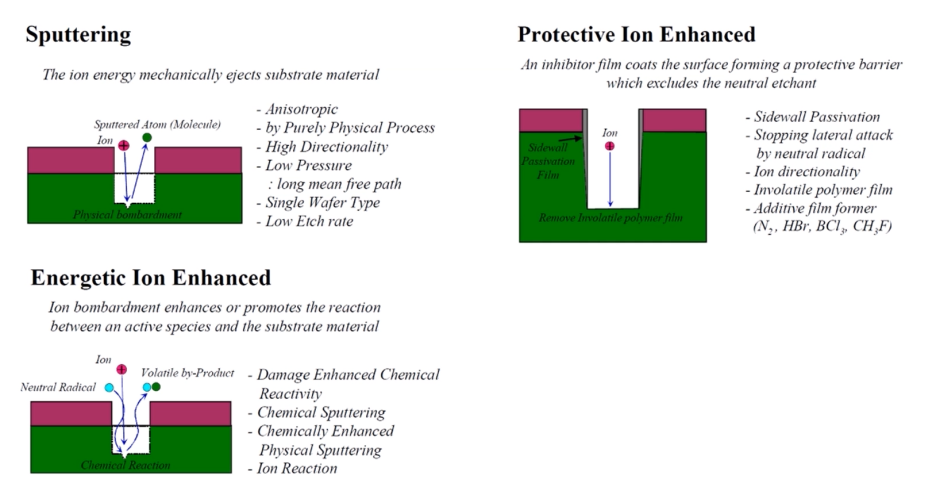
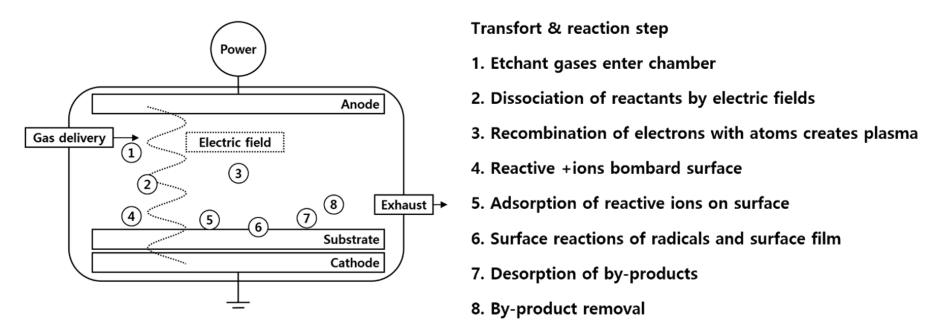
1. MFC를 이용하여 유량 조절
Ashing은 산소 플라즈마를 이용해 PR을 제거
density를 높이는 방법 : 파워를 높이기, 불활성기체를 투입
하지만 파워가 높아지면 이온밀도 필요이상을 높아지거나 자주 충돌하여 열이 발생하여 etch rate감소
'공학 > 반도체' 카테고리의 다른 글
플라즈마 형성 방법 (0) | 2023.06.20 |
---|---|
플라즈마 기초 (0) | 2023.06.20 |
기체 분자 운동론과 진공 (0) | 2023.06.19 |
Etching 공정 : 정의, dry etching 종류, 중요 parameter, 필요요소, 플라즈마 (0) | 2023.06.19 |
플라즈마 사용 공정 : dry etch (0) | 2023.06.19 |
댓글